Khadi: Innovations that Inspire
*Today, August 7th, is celebrated in India as National Handloom Day. The day is marked to elevate the craft of weaving and commemorate the launch of the Swadeshi Proclamation on August 7th, 1905. The Swadeshi Movement in India was ignited to revive national domestic products and drive economic independence for Indian people. It included a boycott of foreign made clothes and goods, driving a regeneration of Indian weaving and practices like Khadi cloth.*
In an ideal setting, the process of making cotton khadi, from seed to fabric, takes place within the village where the cotton is grown.
My first encounter with khadi production in a Gandhian ashram convinced me that this could be achieved. The ashram had a small central production unit located in a little shed, about 20 feet by 40. Fluffy cotton bolls bought directly from farmers were first ginned to separate the seed from the fibres. Next the fibres were carded to separate and clean and roved to make them into slivers, ready for spinning. It all happened through scaled down machines. Humidity levels were self-maintained, reducing the use of power and water.
Spinning was outsourced to women from a working class neighbourhood. They hand-spun the slivers into yarn at home on ‘amber charkhas’– small multi spindle spinning wheels, using the ring frame technology. The yarn was then outsourced to weavers for making khadi.
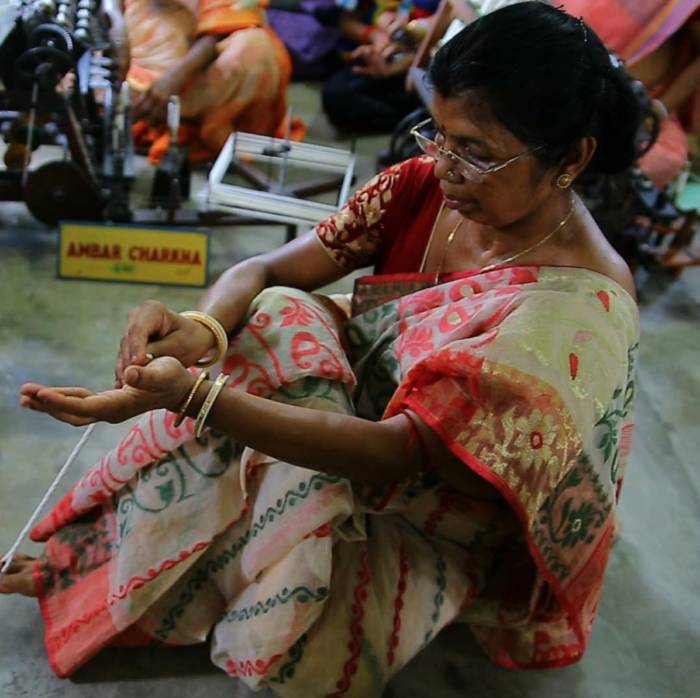
Fast forward to five years ago when we started sourcing khadi for ethically conscious designers in the UK. Early interactions with khadi institutions made me wonder if the idea of small decentralised khadi units might just have been an idealist’s dream. These small khadi units were struggling, with many closing down. The khadi units that had survived tended to be large, governed by bureaucracies and with minimal accountability to spinners and weavers. None of the khadi units were making their own slivers. It turns out that khadi is now made with different rules. To get the official khadi certification, khadi units must use slivers from six central sliver making facilities in India, owned and operated by the same government owned certification agency. Gandhi’s khadi which had helped forge a new national identity to organise communities and to confront British rule seemed to have disappeared.
Fortunately, the disappointment was not long lived. Further explorations led me to innovative initiatives spread across India reinforcing Gandhi’s vision of khadi in a modern context.
Malkha is an early and inspiring example of these innovations. The Malkha journey began in the late 1990’s when Dastkar Andhra, an NGO which was supporting skilled traditional weavers in the southern state of Andhra Pradesh, realised that their efforts to ensure an adequate supply of mill yarn for weavers was leading nowhere.
A search for solutions led to developing their own appropriate technology, with an old abandoned khadi machine as a starting point. Success took years of tinkering, persistence and collaboration. A softer yarn, a result of using cotton bolls and not cotton bales, was a bonus. But this posed further challenges, requiring changes in loom design and persuading weavers to adapt. In the end it all come together, resulting in a unique fabric – Malkha.
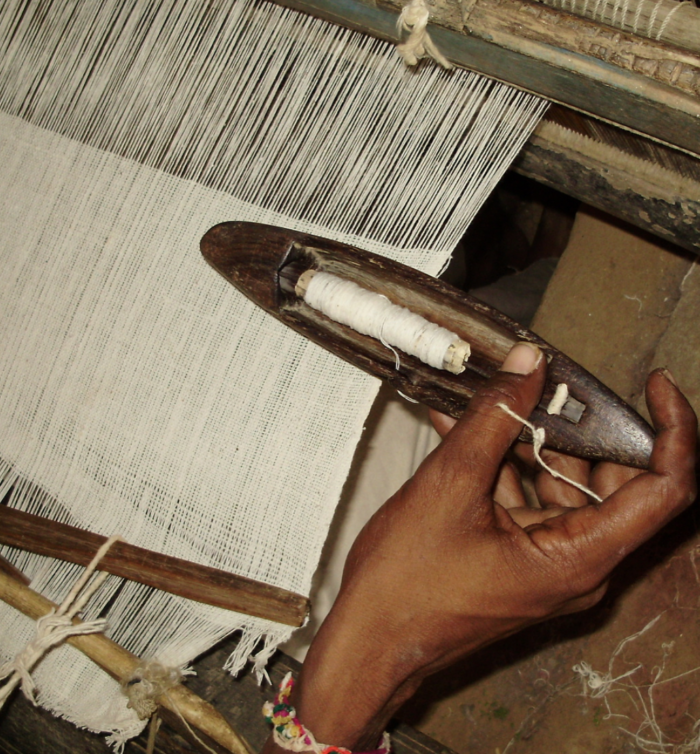
Khamir in the desert district of Kutch in Gujarat has brought a new life to the weavers with the revival of an ancient drought-resistant variety of cotton, kala cotton. Kutch now has its own spinning mill specially designed for processing the short staple kala cotton. Womenweave in Madhya Pradesh has focused on training women weavers, using both khadi and mill yarn. Gopuri is making progress with promoting organic cotton and upgrading old ginning machines and carders. Groups across the country are reviving indigenous cotton varieties and promoting organic farming. Solar technology for small scale textile production is evolving at a rapid pace. There is a momentum for change.
Khadi defined as a dispersed, democratic and decentralised textile production system with zero or low chemical and carbon footprints has the potential to become a force for change. Not just in India but globally.
Learn more at Khadi London.
*This article originally appeared in our latest fanzine: FASHION CRAFT REVOLUTION, a beautifully designed and illustrated 104-page issue that cleverly explains how craft intersects with the identity and culture of communities the world over. Get your copy here and help support all the work we do at Fashion Revolution.*