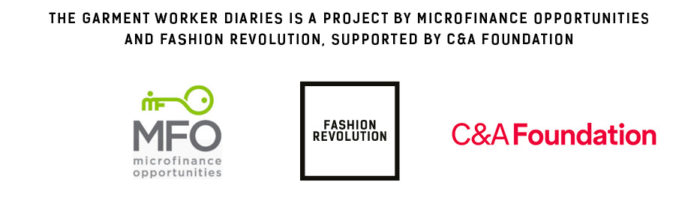
Fashion Revolution’s inaugural Open Studios project was designed to open up the conversation about how clothes are made: to show some of the many processes involved; to give the public who don’t normally have access to the often secretive behind the scenes business of the fashion industry; and to give a platform to some of the designers who are actively finding different ways of producing and selling their collections.
For the designers, this was an opportunity to talk about their clothes and the craftsmanship that goes into making them away from the traditional catwalk format which many new generation designers (and some more established ones) are no longer comfortable with.
A new way of talking about clothes
Fashion is going through a massive shift right now. It’s time to rethink the whole business, from how clothes are made to how they are shown and talked about. Everything is up for question. How many seasons should there be? Is the catwalk show a waste of money (and air miles)? How does a designer communicate most effectively to their community? How does a designer find his or her community?
What is becoming clear is that having an authentic story – whether that’s about the provenance of your materials, the way you make your clothes, your supply chain, or your manufacturing process – resonates with the public. If people trust you and your brand values, they are more likely to become loyal clients.
For young, independent designers, the marketplace is an increasingly crowded one. The gap between the big multi-conglomerate owned brands and independent designers is getting bigger. Even if you have something to say, it is difficult to make your voice heard. But at the same time, the industry is looking for answers and it is the smaller brands who are finding innovative new ways of doing things. Fashion Revolution Open Studios is the perfect place to start those conversations.
Open Studios is an international initiative which is set to expand for 2018. In California, Raquel Allegra hosted a tie-dye workshop in her downtown LA store, showing participants how to dye their own clothes. She also used the opportunity to introduce some of the team who work on the production of her clothes.
Meanwhile, in New York, Audrey Louise Reynolds held an open studio at her Brooklyn Red Hook space showing how she uses vegetable and natural dyes for her delicate pastel pink and turmeric yellow colour palette with advice on how to use her DIY natural dye sachets too. Reynolds has collaborated with Jigsaw as well as Helena Christensen and you can see why her work is in such demand. Read more on WGSN.
And in Jakarta in Indonesia, one of the country’s hottest young designers Wilsen Willim hosted a shirt making workshop at the Indoestri Makerspace. Willim’s signature is the shirt dress which he creates in seemingly endless inventive variations. Willim makes use of the innovative digital startup Kostoom.com which connects him with a network of seamstresses to do his production as piece work which means he, and other small designers, can produce small quantities and scale up or down whilst providing work to tailors working at home.
Studios as creative hubs
Christopher Raeburn embraced the format wholeheartedly. Since moving into his studio space in the old Burberry factory in east London’s Fashion Village, he has been welcoming the public in for studio tours including his archive of vintage military clothing as well as his own collections. He has also started a series of maker workshops where you can learn to cut and sew your own piece of Christopher Raeburn with a little help from his seamstresses and design team. He enjoys welcoming his local community in to see what he is doing.
“I am very proud of my studio,” he said, “and like to open it up as a creative and community hub whenever I can, with regular workshops to teach people how to sew as well as how to repair and customise their clothes and accessories.”
For Open Studios 2017, he hosted a series of open studio tours as well as a “Totes Remade” evening showing guests how to sew their own bag from scrap fabric, and with sponsor Avery Dennison RBIS, created a huge selection box of patches (made from recycled yarn) to decorate the bags. It was quite a party.
“I was very proud to open up the REMADE studio and be a part of Fashion Revolution Week and #whomademyclothes campaign,” said Raeburn. “The tote making workshops were very rewarding events that brought lot of creativity out of the local community.”
Make your own
A real trend that emerged from Open Studios 2017 was a move towards involving the consumer in the process of making their own clothes. Katie Jones held an intimate workshop at her Cockpit Arts space in partnership with Beyond Retro. She taught her participants how to crochet patches to customise or repair existing clothes. It was an opportunity to learn some new skills, meet the designer (and eat lots of Haribos) and learn about her business and craft, but also to make something useful. She’s extending this idea into her practice more and more – keep an eye on her website for in-depth workshops you can join where making your garment is part of the process of owning it. Katie believes that fashion is as much about your relationship with the garment as it is just owning it. It’s not enough to just buy it off the peg (though of course, I’m sure she would welcome that too!) Sign up to get news of her upcoming workshops here
A platform to exchange and share new ideas
As well as workshops as ways to learn a new skill and understand how our clothes are made, Fashion Revolution Open Studios is the ideal platform to discuss and exchange new ideas. We partnered with the Sarabande Foundation for a talk with John Alexander Skelton, one of the most exciting and original new talents to emerge from Central Saint Martins. Skelton looks at his supply chain with forensic detail and creates extraordinary menswear collections using traditional handloom weaving techniques as well as sourcing woven fabrics and knits from local British suppliers. He is forging a new way of producing and selling collections that have, at their heart, an intrinsically ethical and transparent supply chain. Guests were given the rare opportunity to meet John and see his studio, complete with a weaving demonstration. It was a memorable and thought provoking evening, well attended by students, press and industry insiders.
This is Fleur Britten, fashion editor of the Sunday Times’ take on the evening:
The only fashion week worth caring about
There was so much great support and enthusiasm for Fashion Revolution Open Studios 2017, not least from The Debrief who described it as “the only fashion week worth caring about” (we think so, too), as well as Refinery29, Vogue, 10 Magazine, Tank, Sleek, and many others websites and influencers. It was a phenomenal success.
Also taking part in the week’s events were The Autonomous Collections with Kim Stevenson and her ‘ethicool’ workshop where she invited participants to help make a garment; Jodie Ruffle, the extraordinary embroiderer whose recent collaborations have included a project for Adwoa Aboah’s brilliant Gurls Talk Embellished Talk project; Blackhorse Lane Ateliers which hosted a series of open studio events with tours of a unique workshop hand-crafting British made jeans; and the entire textile city of Prato in Italy which staged several workshops and events, coordinated by Italy’s Fashion Revolution country coordinator, the veteran designer Marina Spadafora.
We are in the process of planning Fashion Revolution Open Studios 2018. We have so much to build on, and can’t wait to announce the new line up, hopefully with an event you can take part in near you (or at least online). So stay tuned and thank you for all the amazing support and to all the designers for sharing their stories, their brilliance, and their creativity.
art & eden childrenswear is made by Texport Industries who run a number of social initiatives, trying to improve the lives of their employees and the towns in which they work. Some of their programs include providing additional vocational training for their garment workers, hosting free medical camps every quarter, running a free hospital and employing and supporting differently abled persons.
K. Sreenivasan, Tailor (31 yrs old)
K. Sreenivasan has been working as a tailor at Texport Industries for over ten years. He lives with his wife, Vanitha Mani, and their two children.
Born in Sengottai, India, K. Sreenivasan grew up with his parents and went to a government run school in their town. He later moved to Tirupur to help his grandfather with agricultural work while attending the local government high school.
Similar to the disparity between public and private education in the United States, a large learning and resource gap exists between government run and private education in India. In most cases, if a family can afford to send their children to a private school, they do. As Vikas Bajaj and Jim Yardley reported in their New York Times article on Indian education:
In India, the choice to live outside the faltering grid of government services is usually reserved for the rich or middle class, who can afford private housing compounds, private hospitals and private schools. But as India’s economy has expanded during the past two decades, an increasing number of India’s poor parents are now scraping together money to send their children to low-cost private schools in hopes of helping them escape poverty.
Many government schools struggle to provide adequate electricity, functional resources and educational resources, let alone small class sizes and high quality teaching.
Thus, when K. Sreenivasan joined the workforce instead of going to college at the age of 20, it was a natural next step for him. His parents later joined him in Tirupur and helped him get a job as an office boy. Soon after, he was introduced to Texport Industries where he was hired as a tailor helper. He told us, “Gradually I learned the job of Tailor and gained a thorough knowledge of flatlock, overlock and singer work.”
He married his wife when he was 25 and they went on to have a son and daughter. Today, their son, Deebakkumaran, is eight years old and their daughter, Vidhya, is three.
Despite the lack of access to private education and opportunity, K. Sreenivasan keeps a positive attitude. He is optimistic about the future and finds joy in his daily life.
Every morning, K. Sreenivasan drops Deebakkumaran and Vidhya off at school before continuing on to work. He rides his two-wheeler scooter to the factory, a situation he calls “perfectly suitable because [his] residence is nearby, within 30 minutes!”
K. Sreenivasan takes pride in his work. He told us: “I am a very good tailor. I know flatlock, overlock and singer in all types of machines. [I also] support my team members to execute the buyer’s needs.”
For lunch, K. Sreenivasan rides his scooter home to “take full meals with pure vegetables with [his] family members.” After work, he returns home to help his wife with household duties. Then together they support their kids with homework and get them ready for school the next day. Some evenings, K. Sreenivasan takes his children to Karate and yoga classes, activities he tells us are very popular right now in his hometown.
For his own fun, K. Sreenivasan reads newspapers and watches T.V. “I am always memorizing the film songs and taking my family to the cinema for their entertainment!” he says.
When asked about his ambitions, he said, “My ambition is to make an orphanage home for at least 10 children.” He also added that he wants to make his family cheerful, always!
S. Malar, Checking Department (41 yrs old)
S. Malar has worked at Texport Industries for over six years. She likes the location of the factory because she lives close by, only twenty minutes away. She said the short distance lets her finish all of her housework in the morning and get to the factory in a peaceful manner.
S. Malar was born and raised in Thuraiyur, India where she attended the government girls school up through high school. Like K. Sreenivasan, she began working immediately afterward, doing household work and local jobs in town.
She married at 21, had her first son when she was 23 and had a daughter two years later, a relatively average timeline for many women in India, particularly in smaller, less metropolitan cities. In rural villages and areas where women do not have a chance to receive any education, marriage age can be significantly younger (many are married before 18, the legal marriage age).
Today, S. Malar lives with her husband, son and daughter. Her son, S. Dinesh Kumar, is twenty years old, currently getting his bachelors in mechanical engineering. Her daughter, S. Saranya, is seventeen years old and studying in a school close to their home. Ambitious and determined, S. Malar works hard to give her children the education and opportunities she wasn’t able to have herself. She tells us proudly: “They are the number 1 students in their classes because [in] my after duty hours, I fully engage with them for their studies.” When they aren’t all studying hard, S. Malar spends time with them “by watching T.V., [attending] other cultural programs and supporting them in their basic needs.”
S. Malar has a packed morning during the working week. She has a routine similar to many women responsible for working and running the household. This is what her daily morning schedule looks like:
Even though she has long days and works hard, S. Malar knows she can rely on her and her husband’s combined income to keep them secure. She says: “Our earnings are sufficient for the family’s needs and our children’s education.”
When asked about her ambitions, she said, “My future dream is for our children to become an engineer and lawyer and to improve the status of our family to a better level.”
About art & eden
Susan Correa, founder and CEO of art & eden, has spent her entire career in the apparel industry. She knew first hand the result of low-price competitiveness and quick turn-around pressures in the fashion industry: it created an industry model of as cheap and as fast as possible, no matter the cost. What was that cost?
The environment. The rights and protection of factory workers. Fair wages. Quality materials. Caring for the earth and for the people on it.
When Susan founded art & eden, she was determined to pave a new path, one that was better for people and better for the planet. She refused to hire or collaborate with anyone who didn’t share the same vision, insisting that heart come first, that art & eden be mission-based, not profit-based.
She decided to produce art & eden’s children’s clothing line with Texport Industries after visiting their factories and seeing first-hand their safe, clean and healthy work environment. She was impressed with the positivity and the supportive energy she witnessed at the factory.
Note: The above interviews were conducted by Mr. Ramalingam, Administrative Manager of HR at Texport Industries, and written/transcribed by Nandita Batheja, writer and program facilitator at art & eden.
Authors: Conor Gallagher and Guy Stuart, Microfinance Opportunities
Four years ago today, a fire at the Tazreen Fashions factory outside Dhaka killed 112 garment workers and injured nearly twice as many. In its aftermath, there was an international outcry calling for greater regulation of health and safety conditions in garment factories across the country. Clothing brands and retailers came together and agreed to better monitor conditions inside the garment factories where their clothes are made; and then, after the Rana Plaza disaster, the Bangladeshi government adopted new legislation to strengthen its regulatory body in conducting safety inspections. As of March 2016, the Department of Inspection for Factories and Establishments had inspected 1,549 ready-made garment factories across the country.[1] Despite these steps, workers in garment factories continue to face poor health and safety conditions not only in Bangladesh but in other major garment exporting countries as well. These poor conditions do not necessarily result in major tragedies such as those at the Tazreen Fashions factory or Rana Plaza, but they nevertheless expose the workers in the factories to unsafe conditions and cause them undue pain and suffering.
Through the Garment Worker Diaries project, research teams in Bangladesh, Cambodia, and India have been collecting weekly data on what garment workers earn and buy each week, how they spend their time each day, and whether they experience any harassment, injuries, or other significant events while at the factories. Though we are still in the early stages of data collection, our project covers 540 workers from across these three countries, and we are hearing from them about the health and safety hazards they face.
Workers in our study have informed us about major events that have taken place in the factories. In Bangladesh, women from two different factories have reported fires. In the first case, a fire broke out during their lunch-break, and workers had to put it out themselves. In the second instance, a fire broke out during a midnight shift and took an hour to be extinguished. No casualties were reported in either case.
In Cambodia, one worker informed us that her factory’s owner had not paid their salary, so she ended up going to stand guard at the factory to try and force him to pay. She then filed a complaint in court against the owner in the following week, again asking him to pay. This was more than two months ago, and the situation has still not been resolved. We have seen similar incidents in Bangladesh. For example, six workers from a factory near Dhaka reported a factory-wide strike as the owner had not paid their salaries on time. This resulted in altercations with police officers, pressuring the owner to pay shortly after the fights broke out.
Not all issues that workers face are major events like fires or strikes; workers have been telling us about some more frequent and persistent challenges they deal with too. Workers in our study have reported on repeated harassment in the work place. These incidents range from being yelled at or insulted to sexual harassment. In Cambodia, workers have been willing to share with us the insults they receive. Some examples include women being called “idiots” or “crazy girls,” while one woman’s supervisor told her that she had “no bright future with [her] careless working style.”
Finally, the workers in our study tell us about the pain they endure because of their work. In India and Cambodia, for example, we have found that workers regularly report instances of chronic pain. Respondents in these countries have common ailments: for India, workers commonly experienced back pain. In Cambodia, workers most commonly have reported suffering from headaches. These types of pain are common among garment factory workers who face uncomfortable working conditions that require them to stand in hunched positions performing repetitive tasks for hours on end. Eventually, these conditions wreak havoc on the workers’ bodies, causing the types of chronic pain that our respondents regularly report. In three extreme cases, workers from India reported experiencing back pain every week, and they have reported that this pain can last anywhere from one hour to several days.
We are still in the early stages of collecting and analyzing the data from the 540 women participating in our study. As the Garment Worker Diaries progresses, we will continue to collect information on what is going on inside garment factories in Bangladesh, Cambodia, and India. We will use interviews and surveys to delve deeper into the specific working conditions that workers face.
We now ask you: what would you like to know about the women who make our clothes and the conditions they face at work?
Tell us by tagging us at @fash_rev #workerdiaries
The Garment Worker Diaries is a yearlong research project led by Microfinance Opportunities in collaboration with Fashion Revolution and with support from C&A Foundation. We are collecting data on the lives of garment workers in Bangladesh, Cambodia, and India. Fashion Revolution will use the findings from this project to advocate for changes in consumer and corporate behavior and for policy changes that improve the living and working conditions of garment workers everywhere.
[1] http://database.dife.gov.bd/
Header photo credit: IndustriALL Global Union
On April 24th, 2013, 1,134 garment workers died when an eight-story building, named Rana Plaza, collapsed in Dhaka, Bangladesh. This event marked the beginning of Fashion Revolution Week (April 18-24). It is a time for us to honor garment workers, those who have died in all industrial tragedies in the garment industry, and those who are still suffering in the fashion supply chain today.
At Belvele, we are taking this opportunity to highlight fashion brands who are doing the right thing, by paying fair wages, providing safe working conditions, and treating their talented employees with the respect that they deserve. Although all of our vendors produce ethically, Groceries Apparel and Threads 4 Thought were nice enough to introduce us to some of the people who are making your clothes.
Groceries Apparel
Groceries Apparel operates its own factory in Los Angeles, taking responsibility for their impact on customers, employees, communities and the environment. In addition to ensuring ethical manufacturing, the company uses environmentally conscious materials, such as organic cotton and recycled polyester.
Linda is the pattern maker and a co-founding member of Groceries Apparel, who has been with them for over six years.
Julio is the sew team manager. He has been working at Groceries Apparel for five years.
Threads 4 Thought
Eric and Leigh, the company’s founders, personally travel around the world to find the best Fair-Trade facilities that share their values, and to build relationships with the owners, management, and workers. Their locations include Kenya, India, China, and Haiti. All garments are made with sustainable textiles, such as Organic Cotton, Lenzing Modal, and Recycled Polyester.
Jael works at Wildlife Works in Kenya, one of Threads 4 Thought’s Fair Trade Certified partners, which is located inside an 80K acre wildlife preserve.
Dorothy produces graphic tees and tanks for Threads 4 Thought at Wildlife Works, a carbon-neutral factory which is part of the REDD+ Project, which protects forests, wildlife, and communities in Kenya.
As Fashion Revolution Week approaches, we encourage you to find events near you, and to get involved with the slow fashion movement. Ask your favorite brands on social media, #whomademyclothes to encourage them to be transparent and let them know that you care about their supply chain. With each dollar we spend, we place a vote for the kind of world we want to live in.
Join us on 4/21 for a screening of The True Cost.
Inés is from Mexico and she lived there until one day her uncle —who lived in LA with her aunt at the time— got into a horrible car accident. He was the sole source of income and Inés’ aunt was left with no other option than urge someone from her family come urgently and help. So Inés did. She uprooted everything she knew and left her family and friends. She risked her life to travel to a country she did not know to live on the margins of society and work very hard for little pay, just to help her family survive through a bad patch.
But this is not a story about Inés. This is about thousands of women refugees and immigrants just like her coming to the United States because they have been driven to abandon their home countries in search of a better future. The details change but the themes remain the same. They also have all experienced tremendous hardship. They have all abandoned their homes, families, and the people they love to come here. They have not had the luxury of gaining a good education – most of them do not even have a high school degree or even a GED. They live in such frugal conditions that planning for the future is impossible. And yet, you’d be hard pressed to meet more hopeful women and mothers.
I have heard the stories of their plights repeatedly. These women are at an impasse because without a basic education such as a GED, it’s difficult to get work.
This is why we created Vavavida, to find real solutions to the problems underprivileged women face. Inés is the reason that we exist. But last year, we weren’t helping women like Inés. You see, Vavavida is an ethical fashion e-tailer of beautiful jewelry and accessories that was focused on empowering women’s economic future abroad. We retailed products made by co-ops of artisans in developing countries following the fair trade principles.
Fair trade is quickly becoming the quality standard with commodities like chocolate, coffee, tea and bananas, but it often overlooks workers in first world countries like the United States.
In 2015, we resolved to bring fair trade opportunities to underprivileged women and refugees like Inés here in our home base of San Diego, California. Vavavida partnered with Jennifer Housman, a jewelry designer and a volunteer with PCI to create an artisan co-op of refugees here in the United States. This co-op will give them an opportunity to work from home in conditions where they can work as little or as much as they can any given day and be rewarded with a fair pay for their work. This way, they are empowered to take charge of their own future and do not have to give up money or family time by putting their kids in daycare.
We teach women like Inés to design and make jewelry inspired by the artistic traditions and designs of the regions where they come from. This was our 2015 resolution and we are proud to see the pilot program become a reality. In 2016 we resolve to continue to invest in these women and this program.
What do you resolve for 2016? Please share in the comments section below.
Antoine Didienne is the co-founder of Vavavida, a line of ethically made fashion jewelry items that give back.
1. ) Ethical Fashion & Sustainable Design Summit April 16-18, 2014 | Miami Beach, FL
This Summit is part of Sustainatopia, one of the largest events in the world for social, financial and environmental sustainability. Sponsored by fair trade clothing brandINDIGENOUS and media platform FASHION ONE, the Summit will facilitate a meeting for the entire eco-system of ethical fashion and sustainable design. Spanning the course of three days, 50 international speakers will be featured from various sectors of the industry.
2. ) Copenhagen Fashion Summit April 23-24, 2014 | Copenhagen, Denmark
The world’s largest event on sustainability and fashion, the Copenhagen Fashion Summit will be the platform for leading voices to discuss the fashion industry’s social and environmental responsibility, as well as solutions. The Crown Princess Mary of Denmark hosts and sponsors the event, with the attendance of some of the biggest names in the industry (Livia Firth and Jason Kibbey, to name a few).
3.) Fashion Revolution Day April 24, 2014 | Global
This international movement officially takes off on April 24th when consumers all over the world will be asked, “Who made your clothes?” With events taking place in London, New York, Boston, Israel, Mexico, Japan and more, the day will commemorate the first anniversary of the Rana Plaza factory collapse in Bangladesh. On April 24, wear your clothes#insideout.
4.) ECO Fashion Week April 27-29, 2014 | Vancouver, Canada
The brainchild of founder Myriam Laroche, ECO Fashion Week will take place in its 8th edition in Vancouver. Combining fashion shows with interactive contests, panels and parties, the week is a multi-faceted celebration of sustainably-minded designers and slow fashion as an art form. I attended the event as a speaker last year, and can tell you first-hand, it’s a top-notch event that stands beside any NYFW.
5.) Redress Raleigh May 30, 2014 | Raleigh, NC
Since its inception in 2008, the founders of Redress Raleigh have created a brand that has made a mark both locally and nationally. By connecting and championing eco-conscious designers and companies through event planning and marketing, Redress hosts multiple events throughout the year. Most notably, the Spring Eco-Fashion Show draws speakers, designers, makers and consumers in a conversation about fashion, sustainability and education.
6.) The GreenShows September 2014 | New York, NY
Making a much-anticipated relaunch in September with New York Fashion Week, The GreenShows caters to a community that values beautifully-designed modern apparel that is produced ethically and sustainably, crafted for lasting value, and generating minimal waste. Working with the local, national, and international luxury sustainable fashion community, TGS will host a three-day, world-class Sustainable Fashion Summit including runway shows, resources, symposia, and a short film festival.
7.) SXSW Eco October 6-8, 2014 | Austin, TX
Under the umbrella of the SXSW conference that takes place in March, SXSW Eco attracts a global community to explore, engage and co-create solutions for a sustainable world. Geared towards industry professionals, the three-day event covers many areas of sustainability, fashion included. Attendees are invited to launch startups, pursue marketing opportunities, and apply to showcase designs. With an overarching focus on entrepreneurship, the event is an engaging integration of tech and sustainability.
8.) EcoSessions Year-round | Global
Hosted and founded by Magnifeco’s Kate Black, EcoSessions are popping up around the world to bring together designers, industry and consumers. With discussions about change in behavior, fashion, choice, beauty, materials and living, you won’t want to miss the opportunity to attend a session in your city. All events are free and open to the public.
–
What events are you attending in sustainability and fashion? Leave a comment or tweet me and let me know what I missed.
Reprinted with permission from Shannon Whitehead.
I made this video for Fashion Revolution Day which will be April 24, 2014. To commemorate the one year anniversary of the horribly tragic Rana Plaza collapse. We want everyone to consider the question, Who Made Your Clothes?
You can join the conversation on the FRD Facebook page and make your own video.
As I said in the video above, I really thought this would be easy for me as I’ve invested a great deal of resources, both financially and in terms of research, into having a wardrobe that I can enjoy wearing with a mostly clear conscience. I’ve also made it my job to implore anyone who would listen to simply ask the question, “Where was this made?” or “How was this made?”. So when I chose one of my favorite Jigsaw of London Green Label pieces, I expected to make a complete video.
The folks at Jigsaw were really wonderful! When I got in touch with them, they took my question very seriously. Even though it took several weeks, they did get back to me with a thorough response. I share it with you here:
We here at Jigsaw USA – myself and our head designer Mary included (who created the GL) – believe in a transparent, responsible model. In fact, we’ve created a new division of the GL for just this reason. GL is made from up-cycled fabrics in an effort to limit our footprint on the earth. Due to the nature of these fabrics, it can be tricky to find a specific fabric and/or color if required. When this is the case, we resort to buying fabric from a line, which is obviously not the same as recycling fabric from previous productions. In a concerted effort to remain transparent and provide our customers with an honest product we created Made in US: same contractors, same designs, same quality, different fabrication.
I know you’re interested in who makes our clothes, so let me give you a short run down of how we operate and hopefully I will answer your questions! Both the GL and Made in USA are all made in downtown LA using a handful of small, family-operated manufacturers. They collaborate with us throughout the production life of the garment from design concept through final delivery. As we are a family-owned business, it was important for us to choose small, family-operated manufacturers who have a commitment to quality and share our ethos of a work/life balance.
Each shop is small. The teams of 5-15 have been working together for years and we work directly alongside the patternmakers and sewers on a daily basis. We carefully selected these manufacturers and they carefully selected us! They won’t work with just anyone! We are very fortunate to work with such close knit teams who are a huge part of making Jigsaw GL a truly special endeavor.
So there, you have it! I can now enjoy my Green Label dress even more knowing that it was made collaboratively with a great deal of care for both the people and the garment.
Game on! Pick your favorite piece of clothing and see how easy it is to answer the question. I guarantee you, whether it’s an easy process or a challenge, the experience will be surprisingly gratifying. I’d love to see your video too.
Go ahead, post it on the Facebook page.
It’ll be fun and informative all at once.